When managing electrical systems, it¡¯s crucial to understand the various components that ensure everything runs smoothly and safely. Two commonly encountered terms are power box distribution and electrical panels. Though they may appear similar, these devices serve different purposes in distributing and managing electricity. Understanding the differences between a power box distribution system and an electrical panel can help in making the right choice for your project, whether it¡¯s a temporary setup or a permanent installation.More importantly, put flight case£¬road cases£¬flight case manufacture It is imperative for us to make thorough analysis and maximize its social function. https://sxpowercase.com/product-category/all-product/flight-case/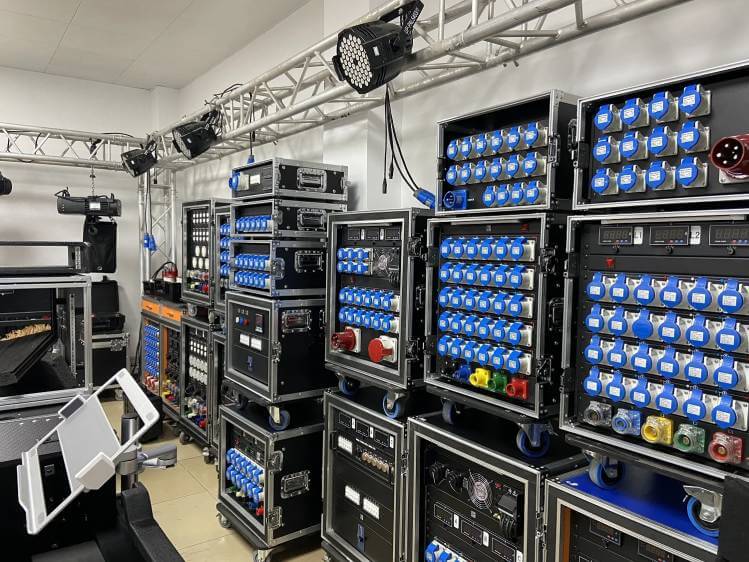
In this blog, we¡¯ll explore the key differences between power box distribution and electrical panels, providing insights into their distinct roles in power distribution and safety.
What is Power Box Distribution?
A power box distribution system, also known as a portable power box or distro box, is a temporary power distribution unit used in settings like construction sites, events, or outdoor locations. These boxes are designed for portability and can be easily transported to different locations where temporary electrical setups are needed.
Key Features of Power Box Distribution:
Portability: Power box distribution units are compact and designed for mobility, making them ideal for temporary setups.
Multiple Outputs: They offer various output connectors, allowing users to distribute power to multiple devices from a single source.
Safety Features: Power boxes often include circuit breakers, ground fault protection, and overload protection to ensure safe operations.
Power box distribution systems are highly useful in environments where flexibility and rapid deployment are necessary, such as at live events or in industrial settings that lack a permanent power source.
Video Player
00:00
00:30
What is an Electrical Panel?
An electrical panel, also known as a breaker panel or main distribution board, is a fixed system that serves as the central hub for distributing electricity throughout a building. Connected to the main power supply, the panel divides electricity into individual circuits, each serving specific areas or devices within the building. It also contains circuit breakers or fuses to prevent overloads and ensure electrical safety.
Key Features of an Electrical Panel:
Permanent Installation: Electrical panels are permanently installed in homes, commercial buildings, or industrial facilities.
Centralized Power Management: The panel controls the distribution of electricity throughout a building, directing power to lighting, appliances, or other electrical systems.
Circuit Protection: Electrical panels include circuit breakers that automatically shut off power in the event of an overload or short circuit, enhancing safety.
Electrical panels are vital for maintaining safe and efficient power distribution in buildings, ensuring that electricity flows where it¡¯s needed while preventing dangerous situations like overloads.
Differences Between Power Box Distribution and Electrical Panels
While both systems manage power distribution, they have distinct roles and functionalities. Here are the main differences:
1. Portability vs. Permanent Installation
The primary distinction between power box distribution and electrical panels lies in their portability. Power boxes are portable, designed to be moved from one location to another. In contrast, an electrical panel is permanently installed in a building and remains in place throughout its usage.
2. Temporary vs. Permanent Power Needs
Power distro box is typically used for temporary setups, such as at events or on construction sites. In contrast, electrical panels are designed for long-term power distribution within buildings, providing a stable infrastructure that rarely changes over time.
3. Circuit Capacity
Electrical panels generally support a greater number of circuits compared to power boxes. While an electrical panel manages power distribution across an entire building, a power box is used to distribute electricity to specific areas or devices for short-term applications.
4. Safety and Circuit Protection
Both systems offer circuit protection, but the complexity of the protection may differ. Electrical panels often include more sophisticated safety measures, as they are responsible for the power needs of an entire building. Power boxes, while also equipped with safety features like breakers, are designed for more immediate, flexible needs.
5. Use Cases
Power Box Distribution: Ideal for temporary events, mobile setups, construction sites, or any location requiring a flexible power solution.
Electrical Panels: Designed for permanent installation in homes, commercial buildings, and industrial facilities where consistent power distribution is required.
When to Choose Power Box Distribution
Power box distribution systems are the go-to choice for environments where temporary and portable power solutions are needed. For example:
Outdoor Events: Concerts, festivals, or exhibitions often require temporary electrical setups, making power boxes essential.
Construction Sites: These boxes are frequently used to power heavy equipment and tools in areas without established electrical infrastructure.
Film and TV Productions: Power boxes are used to supply electricity to lighting, sound equipment, and other devices on sets.
In these cases, portability and ease of setup are crucial, and power boxes offer the flexibility needed for efficient power distribution.
When to Choose an Electrical Panel
For long-term, permanent power distribution, an electrical panel is the best choice. It¡¯s commonly used in:
Homes: Residential buildings rely on electrical panels to distribute power to all areas, from lighting to appliances.
Commercial Buildings: Offices, retail spaces, and other commercial properties need electrical panels to manage their power needs safely and efficiently.
Industrial Facilities: Large-scale industrial operations require robust electrical panels for distributing power across machinery, lighting, and other critical systems.
Conclusion
Both power distro box systems and electrical panels play essential roles in distributing electricity, but their use cases differ significantly. Power boxes are built for portability and flexibility, making them perfect for temporary setups, while electrical panels offer permanent, long-term power solutions for buildings.
For those in need of reliable, temporary power solutions, SX offers top-of-the-line power distro box . Whether you¡¯re managing a large-scale event, a construction site, or a film production, SX ensures that your power needs are met safely and efficiently. With SX¡¯s expertise in providing portable and robust power solutions, you can ensure a seamless power distribution experience, whether you need a flight case or a power box.